Our Mission
About Us – Monocure3D develops, manufactures, and supplies high-quality 3D printing products to consumers, businesses, and resellers. As a company solely focused on the 3D printing industry, we provide expert technical support, reliable products, and in-depth education to help our customers achieve the best results. Our commitment to innovation and quality ensures that every product meets the highest standards, making 3D printing more accessible and efficient for all users.
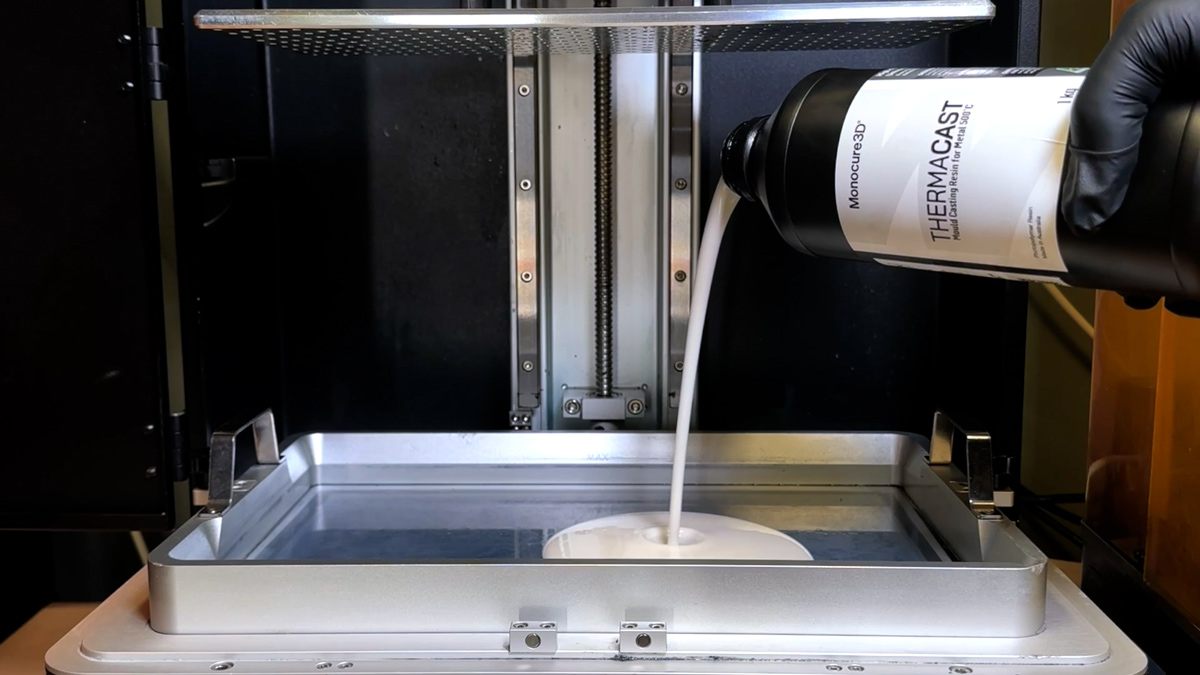
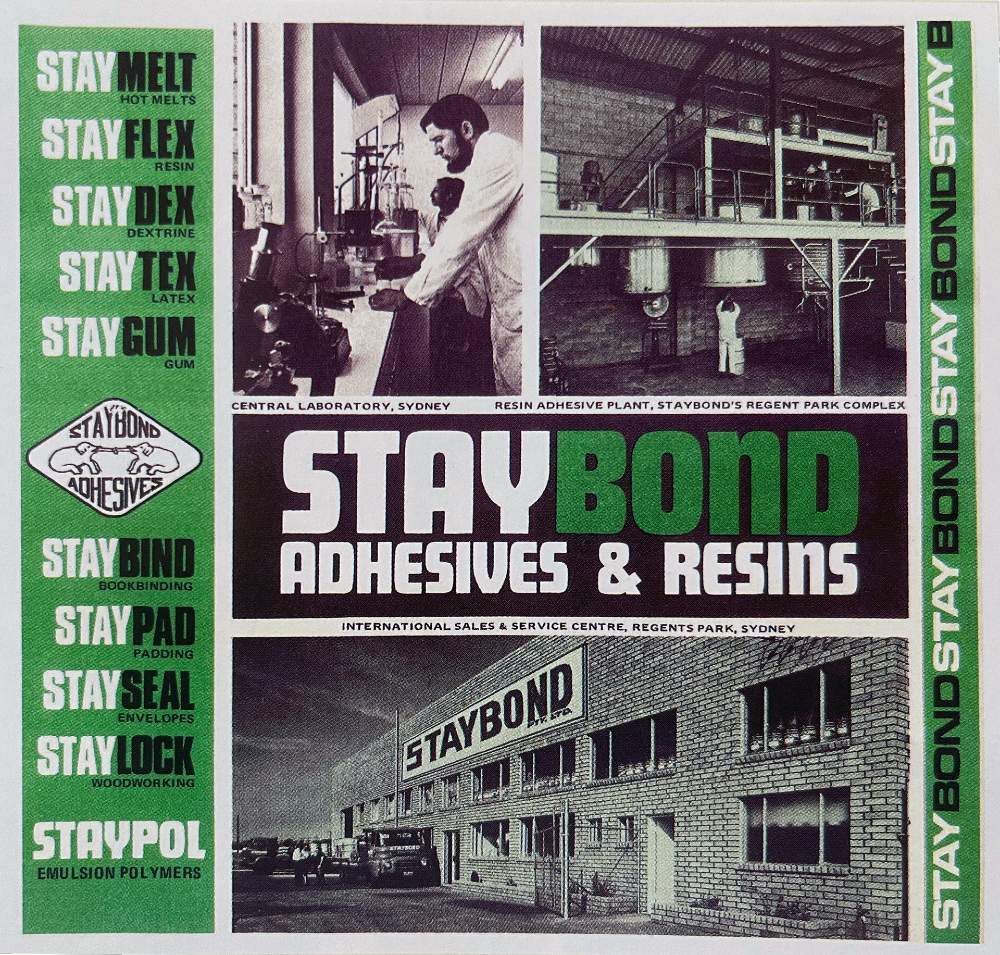
Our History
Monocure Pty Ltd was founded in 1979 by Alan Anderson as an extension of his adhesives company, Staybond Pty Ltd, after it was acquired by a multinational corporation. Initially established as an industrial chemical development and manufacturing company, Monocure specialised in producing UV-cured inks for the printing, packaging, and label industries.
Nearly 40 years later, in 2016, our Chief Development Chemist, Kevin Jarrett—a founding team member—developed Australia’s first resin for SLA, DLP, and MSLA 3D printers. Recognising the potential of 3D printing as an emerging and transformative industry, Monocure3D was born, marking a new chapter in our company’s journey.
Today, Alan’s son, Charlie, leads Monocure3D, keeping it a 100% family-owned and operated business. His passion for 3D printing, innovation, and the thriving maker community continues to drive the company forward.
With a strong foundation in research, development, and manufacturing, Monocure3D remains at the forefront of 3D printing technology worldwide, delivering high-quality materials and pioneering new solutions for the industry. The future is bright, and we’re excited to keep pushing boundaries in additive manufacturing.
Product Development
We actively engage with the 3D printing community through support chats, social media groups, surveys, and courses. This direct involvement gives us a deep understanding of the challenges and needs of 3D printers worldwide, allowing us to develop practical, high-quality solutions that truly make a difference.
Our focus is on creating products that enhance your 3D printing experience. From formulating our own base resins to ensuring competitive pricing, we work tirelessly to deliver unique, reliable, and cost-effective solutions.
Every new product undergoes rigorous testing, including independent field trials, before launch. This ensures that what you receive performs exactly as described. Explore our full range of products in the shop section of this website.
In-House Manufacturing
Keeping our manufacturing in-house ensures faster communication, eliminating issues like language barriers and time-zone delays. It also means you get the products you need, when you need them—without the risk of shipping delays or stock shortages disrupting your workflow.
With over 30 in-house product lines, we proudly supply customers in more than 30 countries worldwide. Our purpose-built facility in Sydney, Australia, is designed specifically for the development and production of high-quality 3D printing materials.
If you’re ever in Sydney, we’d love to show you around! Contact us to arrange a tour of our facilities and see firsthand how we create the products that power your 3D printing projects.
Quality Control
At Monocure3D, we focus on results. Our philosophy is simple: “What you put in is what you get out.”
We know that detail, strength, and durability matter to you. That’s why we subject our products to strict quality control, adhering to ISO 9001 accreditation guidelines.
Every batch undergoes rigorous lab testing, where it is compared against previous batches to ensure consistency. We then test it on standard 3D printers to verify performance. This meticulous process guarantees that every bottle of resin you receive delivers the same reliable quality as the last.
Our Partners
To provide the best customer experience, we partner with industry-leading logistics providers.
We’ve carefully selected DHL, Australia Post, StarTrack, CBD Couriers and Vanguard Logistics (for sea freight) to ensure your orders arrive on time and in excellent condition. Combined with our growing network of local resellers, we provide our products, which are available worldwide.
Interested in becoming a reseller? Fill out our reseller application form to join our growing global family—we’ll be in touch as soon as possible!
We also support businesses by offering generous volume-based wholesale discounts. If you’re interested in using Monocure3D products in your business, start by submitting a wholesale application form today.
3D Printer Technology
3D printing, also known as additive manufacturing, uses computer-aided design (CAD) to create three-dimensional objects through a precise layering process. This technology builds objects by depositing materials layer by layer, including plastics, composites, resins, and bio-materials. The result is highly detailed, customisable objects that vary in shape, size, rigidity, and colour, making 3D printing a versatile solution across multiple industries.
What are the different types of Resin 3D Printers?
The term “stereolithography” originates from the Greek words “stereo,” meaning solid, and ”(photo)lithography,” referring to a method of ‘writing’ with light. Stereolithography (SLA) 3D printing does exactly that—drawing solid objects with light, one layer at a time.
There are three main types of SLA processes:
• Laser-based stereolithography (SLA)
• Digital Light Processing (DLP)
• Masked SLA (MSLA)
In all these processes, a vat of photo-reactive liquid resin is selectively exposed to light, solidifying thin layers that build up to form a complete 3D object.
While laser-based SLA, DLP, and MSLA share the same fundamental technology, they can produce significantly different results. Understanding their key differences will help you decide which printing method best suits your needs. By optimising your production workflow for each type of printer, you can achieve higher efficiency, better accuracy, and superior print quality.
Resin-Based SLA & DLP 3D Printers
Laser-based SLA was Charles Hull’s first stereolithography technology, developed in 1986. It uses a UV laser to trace and solidify each layer of an object. Two motor-driven mirrors (galvanometers or ‘galvos’) direct the laser along the X and Y axes, curing the resin as it moves.
Examples: Formlabs Form 2 & Form 3
DLP (Digital Light Processing) uses a digital projector to expose an entire layer simultaneously, making it faster than laser SLA. Since the image is pixel-based, layers are made of small rectangular bricks called voxels, which stack along the Z-axis.
Examples: Asiga Ultra & Sprintray 95S DLP
MSLA Technology
Masked SLA (MSLA) uses an LED array as a light source and an LCD photomask to shape the image of each layer. Like DLP, the LCD photomask is pixel-based, but the pixel size varies depending on the LCD resolution.
During printing, individual pixels on the LCD are deactivated to allow light to pass through and cure the resin. Unlike DLP, where XY accuracy depends on lens scaling, MSLA has a fixed XY resolution determined by the LCD panel.
Examples: Anycubic, Elegoo, Creality, Phrozen, Uniformation.