Monocure3D’s Manufacturing and Quality Control Procedures
At Monocure3D, consistency and quality are at the heart of everything. I’m Lina, the Product Manager and Quality Control Supervisor at Monocure HQ, and I’m excited to share an inside look at the meticulous processes we follow. Every step of our manufacturing and quality control workflow is designed to ensure our 3D printing resins meet the highest performance and reliability standards, giving our customers confidence with every print.
Batch-to-Batch Consistency: Our Priority
We take batch-to-batch consistency very seriously when manufacturing our 3D printing resins. Each batch is produced using carefully developed formulas, recorded in a “batch card.” This card outlines every process step, from weighing raw materials to final blending, ensuring strict adherence to our ISO9001 quality management guidelines.
Raw materials are precisely weighed and blended during production using a high-speed mixer. This precision ensures uniformity and accuracy across the entire batch, reducing the variability risk. Our production team rigorously follows these procedures to create consistent, high-quality resins every time. By maintaining these exacting standards, we deliver products that perform flawlessly, whether for intricate models or demanding industrial applications.
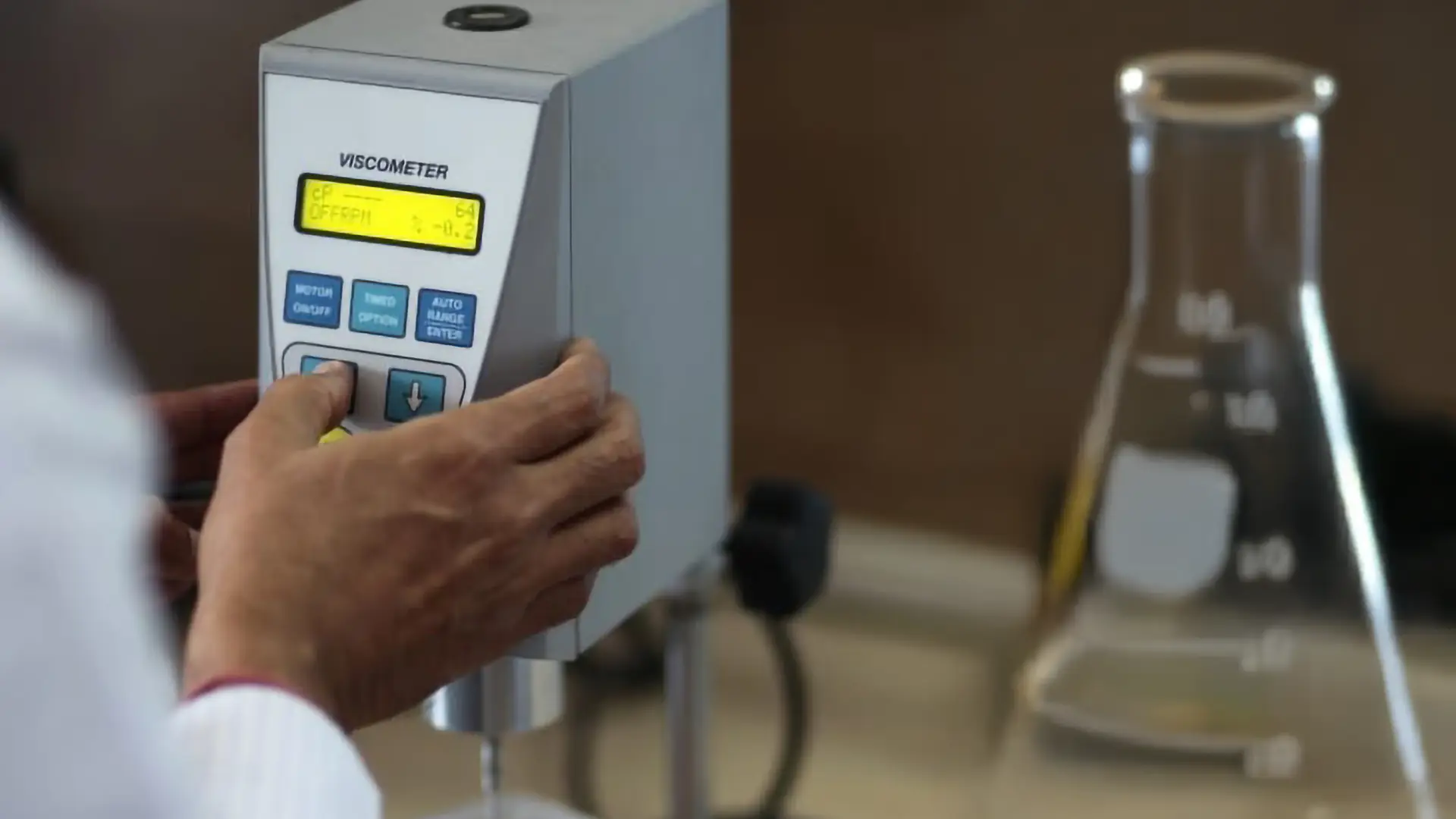
Rigorous Testing by Quality Control Chemists
Once a batch is manufactured, it undergoes a thorough testing process in one of our laboratories. A fully qualified Quality Control Chemist conducts these tests to ensure the resin meets a predetermined set of criteria, matching it against a retained sample from the previous batch.
To confirm consistency, the testing process evaluates key factors such as viscosity, reactivity, and physical properties. If any deviations are detected—such as a slightly higher or lower viscosity—the chemist authorises adjustments to the batch. This iterative process is repeated until the chemist and I are happy with the product’s performance.
A viscometer is a device used to measure the viscosity of a fluid, which is its resistance to flow. It determines how the fluid reacts to applied forces, such as shear or gravity. Standard viscometers include rotational viscometers, which measure the torque required to rotate an object in the fluid, and capillary viscometers, which calculate viscosity based on the time it takes to flow through a narrow tube. These tools are essential in industries like 3D resin manufacturing, where consistent viscosity ensures product quality and performance.
“Every step of our manufacturing and quality control workflow is designed to ensure our 3D printing resins meet the highest standards of performance and reliability, giving our customers confidence with every print.”
Ensuring Print Quality
A batch isn’t approved until it passes a complete 3D printing test. This process involves printing a carefully designed test model that evaluates critical performance metrics such as layer adhesion, dimensional accuracy, and surface finish. The model is inspected for inconsistencies or defects to ensure the resin meets functional and aesthetic standards. This step replicates real-world applications, giving us confidence that the resin will deliver optimal results for our customers. Only after passing this rigorous test can the batch be cleared for final processing, ensuring every bottle of resin we produce performs flawlessly in 3D printing environments.
Controlled Filling, Filtering, and Packaging
Once a batch is approved, it moves to our advanced filling line, where an additional filtration step is performed using a fine-micron filter. This removes any remaining microscopic impurities, guaranteeing a pure, consistent product. The resin is then carefully measured, filled, and capped in our environmentally controlled facility. This controlled environment helps protect the resin from contamination, UV exposure, and temperature fluctuations during packaging. Finally, each bottle is meticulously labelled to ensure traceability, providing customers with all the necessary product and batch information. These steps combine precision and care to deliver a product that meets the highest standards of quality and reliability.
Our Commitment to Quality
At Monocure3D, we take pride in our commitment to producing consistent, high-quality resins for 3D printing. Every batch reflects the hard work, expertise, and attention to detail our team invests in creating trustworthy products.
If you have any questions about our process or would like more information about our products, feel free to get in touch—we’re always happy to share more about what makes Monocure3D stand out.
“We take batch-to-batch consistency very seriously, using carefully developed formulas and rigorous ISO9001 guidelines to guarantee every product meets our exacting standards.”